Perforated metal holds significant importance in the automotive sector. This article delves into its diverse applications within the industry, highlighting its advantages, variations, and customization possibilities.
Importance of Perforated Sheets in Automotive Manufacturing
Perforated sheets offer numerous benefits in automotive manufacturing, including durability, aesthetic appeal, and functional advantages. These sheets enhance vehicle performance by providing solutions for cooling, noise reduction, and structural integrity.
Enhancing Cooling Efficiency
Perforated sheets improve cooling efficiency in vehicles. They act as heat shields and grilles, allowing airflow to cool essential components like engines and exhaust systems. This reduces the risk of overheating and enhances overall vehicle performance.
Noise Reduction
Perforated metal plays a significant role in noise reduction. By incorporating perforated sheets in the design of mufflers and soundproofing panels, manufacturers can significantly reduce engine and road noise, providing a quieter ride for passengers.
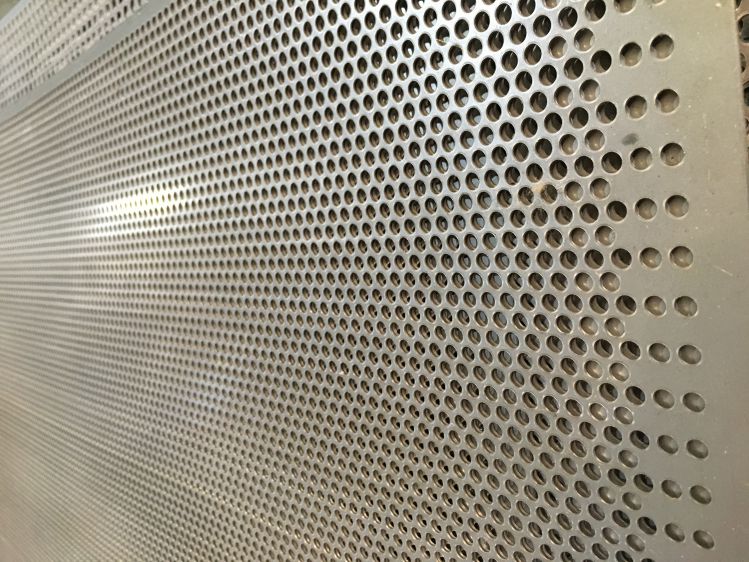
Types of Perforated Metal Used in Automotive Manufacturing
Various types of perforated metals are used in automotive applications. Each type offers unique properties that make it suitable for specific uses.
Stainless Steel Perforated Sheets
Stainless steel perforated sheets are favored for their strength, durability, and resistance to corrosion. These sheets are commonly used in exhaust systems, grilles, and heat shields due to their ability to withstand high temperatures and harsh conditions.
Aluminum Perforated Sheets
Aluminum perforated sheets are lightweight and resistant to corrosion, making them ideal for applications where weight reduction is crucial. They are often used in vehicle body panels, interior trim, and other components where weight savings can improve fuel efficiency.
Carbon Steel Perforated Sheets
Carbon steel perforated sheets offer excellent strength and durability, making them suitable for heavy-duty applications. These sheets are used in structural components, underbody shields, and other areas that require high strength and impact resistance.
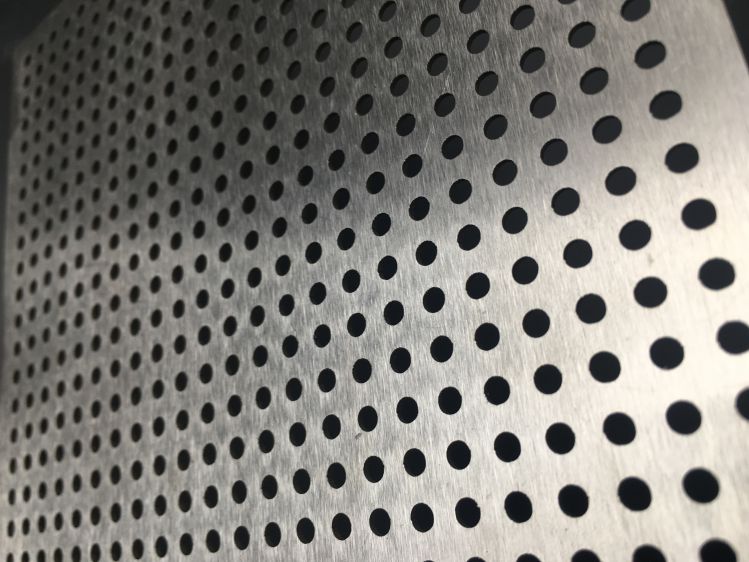
Key Applications of Perforated Metal in Automotive Manufacturing
Perforated metal finds applications in various aspects of automotive manufacturing, contributing to the performance, safety, and aesthetics of vehicles.
Engine and Radiator Grilles
Perforated sheets are commonly used in the design of engine and radiator grilles. These grilles allow for efficient airflow while protecting critical components from debris and damage. The durability and customizable patterns of perforated sheets make them ideal for these applications.
Exhaust Systems
Perforated metal is essential in the construction of exhaust systems. It is used to create components such as mufflers and heat shields that require high heat resistance and noise reduction properties. The perforated design allows for effective sound attenuation while maintaining structural integrity.
Interior Trim and Panels
In vehicle interiors, perforated sheets are used to create aesthetically pleasing and functional trim panels. These sheets provide a modern look while allowing for airflow and sound absorption, enhancing passenger comfort.
Safety Features
Perforated metal is also utilized in various safety features within vehicles. This includes components like guard plates, protective shields, and impact-absorbing panels that enhance passenger safety by providing additional protection in case of accidents.
Benefits of Using Perforated Sheets in Automotive Manufacturing
The use of perforated sheets in automotive manufacturing offers several benefits that enhance vehicle performance and safety.
Improved Airflow
Perforated sheets enable improved airflow in various vehicle components, such as radiators, engines, and exhaust systems. This efficient airflow helps maintain optimal operating temperatures, reducing the risk of overheating and improving overall performance.
Noise Reduction
By incorporating perforated metal in mufflers and soundproofing panels, manufacturers can achieve significant noise reduction. This enhances passenger comfort by providing a quieter cabin environment.
Lightweight Solutions
Using lightweight materials like aluminum perforated sheets contributes to overall vehicle weight reduction. This improvement enhances fuel efficiency and performance, making vehicles more eco-friendly and cost-effective.
Durability and Corrosion Resistance
Perforated sheets made from materials like stainless steel and aluminum offer excellent durability and resistance to corrosion. These properties ensure that components remain functional and aesthetically pleasing even under harsh conditions.
Customization Options for Perforated Sheets in Automotive Manufacturing
Custom Patterns and Designs
Manufacturers can customize perforated sheets with various patterns and designs to meet specific aesthetic and functional requirements. This flexibility allows for unique styling options and enhanced performance characteristics.
Material Selection
Perforated sheets can be made from different materials, including stainless steel, aluminum, and carbon steel, depending on the application’s requirements. This variety ensures that the selected material offers the best combination of strength, weight, and durability.
Finishing Options
Various finishing options, such as powder coating and anodizing, can be applied to perforated sheets to enhance their appearance and resistance to corrosion. These finishes also add an extra layer of protection, extending the lifespan of the components.
Environmental Impact and Sustainability
Using perforated metal in automotive manufacturing contributes to sustainability and environmental protection. The materials used, such as aluminum and stainless steel, are recyclable, reducing waste and conserving resources.
Recyclability
Perforated metal components are fully recyclable, allowing for the reuse of materials and reducing the need for raw material extraction. This recyclability helps minimize the environmental impact of automotive manufacturing.
Energy Efficiency
Lightweight perforated sheets contribute to overall vehicle weight reduction, improving fuel efficiency and reducing greenhouse gas emissions. This energy efficiency aligns with global efforts to reduce the environmental impact of transportation.
Future Trends in Perforated Metal Applications
The use of perforated metal in automotive manufacturing is expected to grow, driven by advancements in materials science and manufacturing technologies.
Advanced Materials
The development of advanced materials, such as high-strength alloys and composites, will expand the range of applications for perforated metal in automotive manufacturing. These materials offer improved performance characteristics, making them suitable for more demanding applications.
Innovative Manufacturing Techniques
Advancements in manufacturing techniques, such as additive manufacturing and precision laser cutting, will enable the production of more complex and precise perforated metal components. These innovations will enhance the design flexibility and performance of automotive components.
Customize Your Perforated Sheets from Our Factory
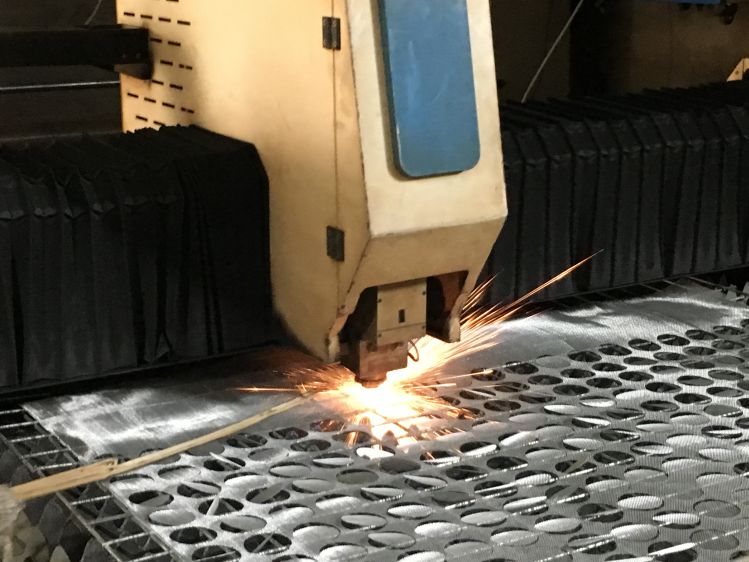
Overview of the Customization Process
Our customization process ensures each perforated sheet meets the unique requirements of our clients:
- Consultation: Understand your specific needs and preferences through detailed consultation.
- Design: Create detailed plans based on your specifications, ensuring a perfect fit and optimal performance.
- Production: Utilize advanced manufacturing techniques to produce customized perforated sheets to exacting standards.
- Quality Control: Perform rigorous quality checks to ensure high standards.
- Delivery: Handle all logistics aspects to ensure timely delivery to your location.
Benefits of Custom Solutions
Customizing perforated sheets provides several benefits:
- Perfect Fit: Ensure a perfect fit for your facility’s components with custom sizes and shapes.
- Enhanced Durability: Tailored materials and designs enhance durability and performance.
- Unique Aesthetic: Match specific aesthetic requirements of your facility with custom finishes and patterns.
- Operational Efficiency: Address specific operational challenges with custom solutions, improving overall efficiency.
After-Sales Service
Reliable after-sales service ensures long-term relationships with our clients. Our after-sales service includes:
- Technical Support: Provide ongoing technical support to ensure optimal product performance.
- Maintenance Guidance: Offer detailed maintenance guides to help clients keep their perforated sheets in top condition.
- Replacement Parts: Provide quick access to replacement parts to minimize downtime and maintain operational efficiency.
- Customer Feedback: Actively seek and incorporate customer feedback to continually improve our products and services.
Contact Us
Enterprise customers interested in custom perforated sheets can contact us by submitting the form on our website. Our team stands ready to assist you with your specific needs and provide tailored solutions that enhance the functionality and appearance of your automotive components.